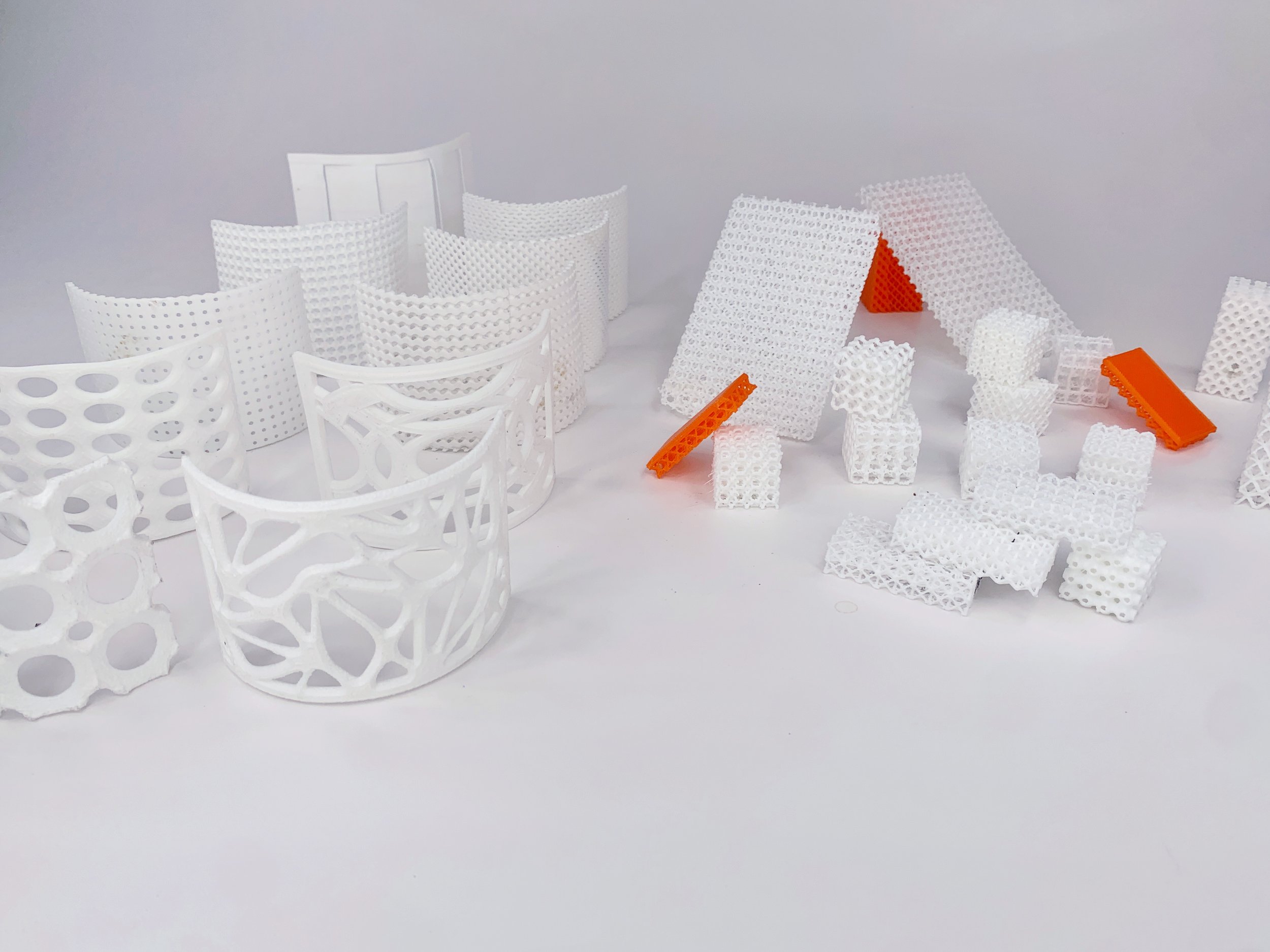
Textile Infused 3D Printing
Reimagined Sports Protection System - Process & Background
Scroll ↓
The musty smell of sweaty sports equipment is a common locker room issue. Traditional protective gear often uses non-permeable materials, trapping moisture and fostering odor-causing bacteria.
Our team is rethinking sports equipment by focusing on breathability, comfort, and protection. We use breathable textiles and multi-material thermoplastic deposition (FDM) to create a composite that enhances flexibility and comfort while maintaining safety.
We started the ideation process by thinking about different ways to innovate with additive manufacturing. This lead us to our breathable lattice padding concept.
Moisture-wicking fabric draws sweat away from the skin, and when paired with breathable padding, it promotes evaporative cooling and prevents stagnant moisture. This combination keeps equipment odor-free.
Prototyping and Testing
To start, we tested different lattice structures to assess the qualities of each. By dropping weights on the lattices and testing the airflow through the lattice, we were able to see which structure absorbed the most impact and was the most breathable. This helped us choose the most effective geometry for the padding of the shin guard.
Colorways
After prototyping we came to a final design that prevents smell and bacteria growth without sacrificing protection.
However, the demonstration of this system is only the beginning, and could be modified and applied to other types of padding seen below.
Ideation & Concept Development
Moisture Wicking Fabric
The textile element provides a more comfortable interface for the skin, and moisture wicking.
Full System Breakdown
Breathable lattice
Made of TPU, the lattice offers the energy absorption of traditional foams without the drawbacks. Its open-air design allows the the textile to perform, instead of suffocating it.
Protective shell
Made of carbonfiber peek, fiberglass peek, or other composites, this layer offers offers protection and a visual identity that speaks to the consumer.
Next, we tested different shell structures for rigidity, airflow, and visual association. To test this, we put the lattice behind the shell, put it on our shin, and hit each other with a metal water bottle. This simulated getting kicked in the shin, and allowed us to understand the properties of each shell.
From here we were able to combine the lattice and shell we found most effective and test the full system.